CGL(Continuous Galvanizing Line) process Heating Furnace
Enhancing Quality Competitiveness
AS-IS
•
Difficult to check properties due to changes in operating conditions and taking 2-3 hours to confirm defects
•
Variations in operating methods by operators due to the absence of standardized operating procedures
•
Challenges in temperature control of the furnace settings according to speed changes
INFINITE OPTIMAL SERIES™
•
Improved manufacturing quality by reducing the error between target settings and actual measurements for each steel type
•
Reduce operating deviations by operator
•
Reduce LNG usage
T0-BE
•
25% reduction in exit temperature prediction error
•
Annual fuel cost savings of $50 million
•
Increase in molten steel production
•
Stabilization of blast furnace operation
Key data
•
Property target values, speed, time, production quantity, etc.
※ Actual data required for implementation may vary.
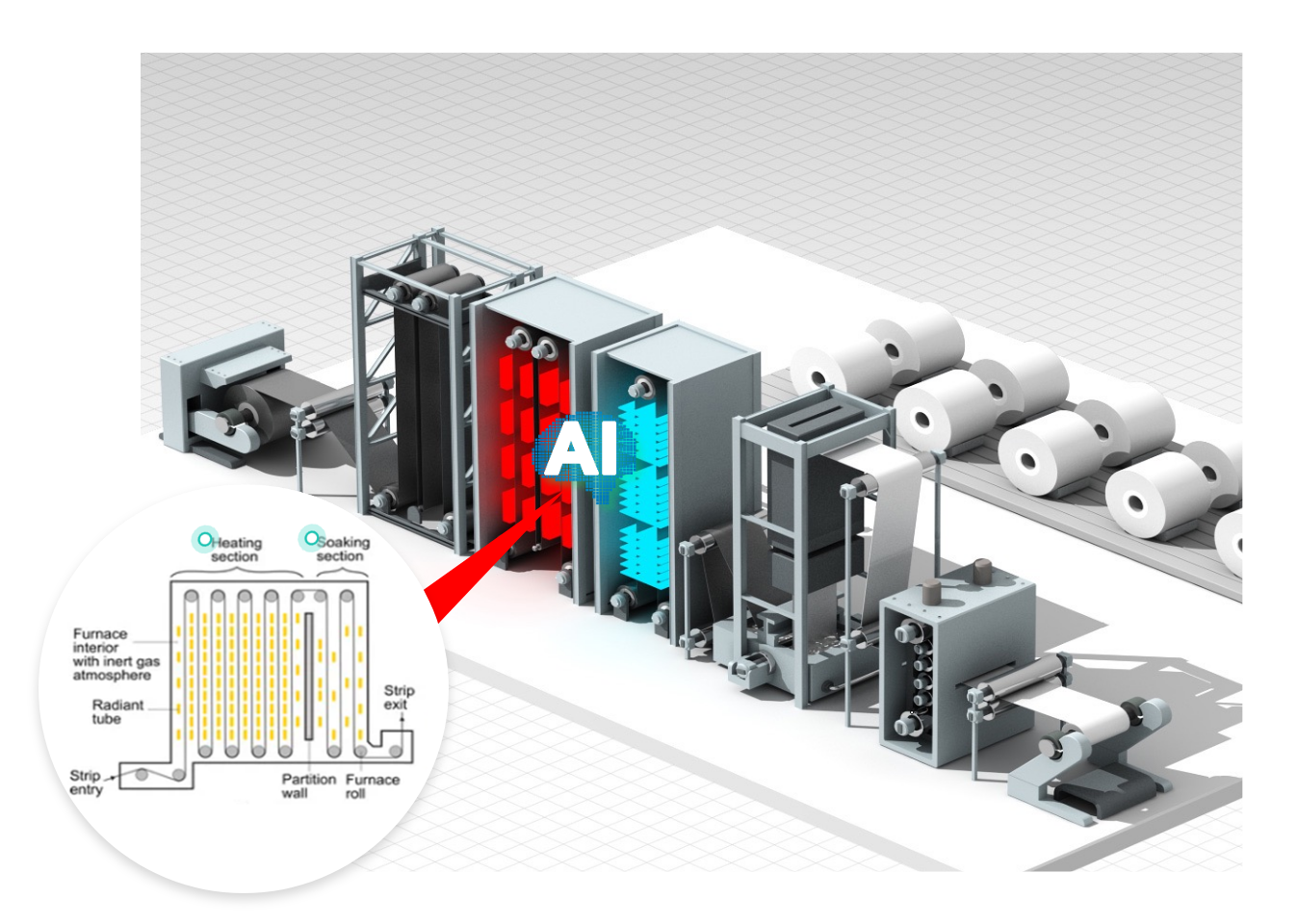
Steelmaking process Electric Furnace
Increasing productivity and reducing electric power usage
AS-IS
•
Difficult to confirm the melting state of scrap due to the high temperature inside the furnace
•
Variations in production quantities exist due to different operating methods by individual workers
INFINITE OPTIMAL SERIES™
•
Stabilization of production through accurate prediction of scrap melting
T0-BE
•
Productivity improvement of over 3%
•
Reduction in power consumption of over 2%
•
Estimated annual fuel cost savings of $0.6 million (as of 2021)
Key data
•
Scrap weight, Item ratio, Electric power supply time, The number of operators, Operating time by operator
※ Actual data required for implementation may vary.
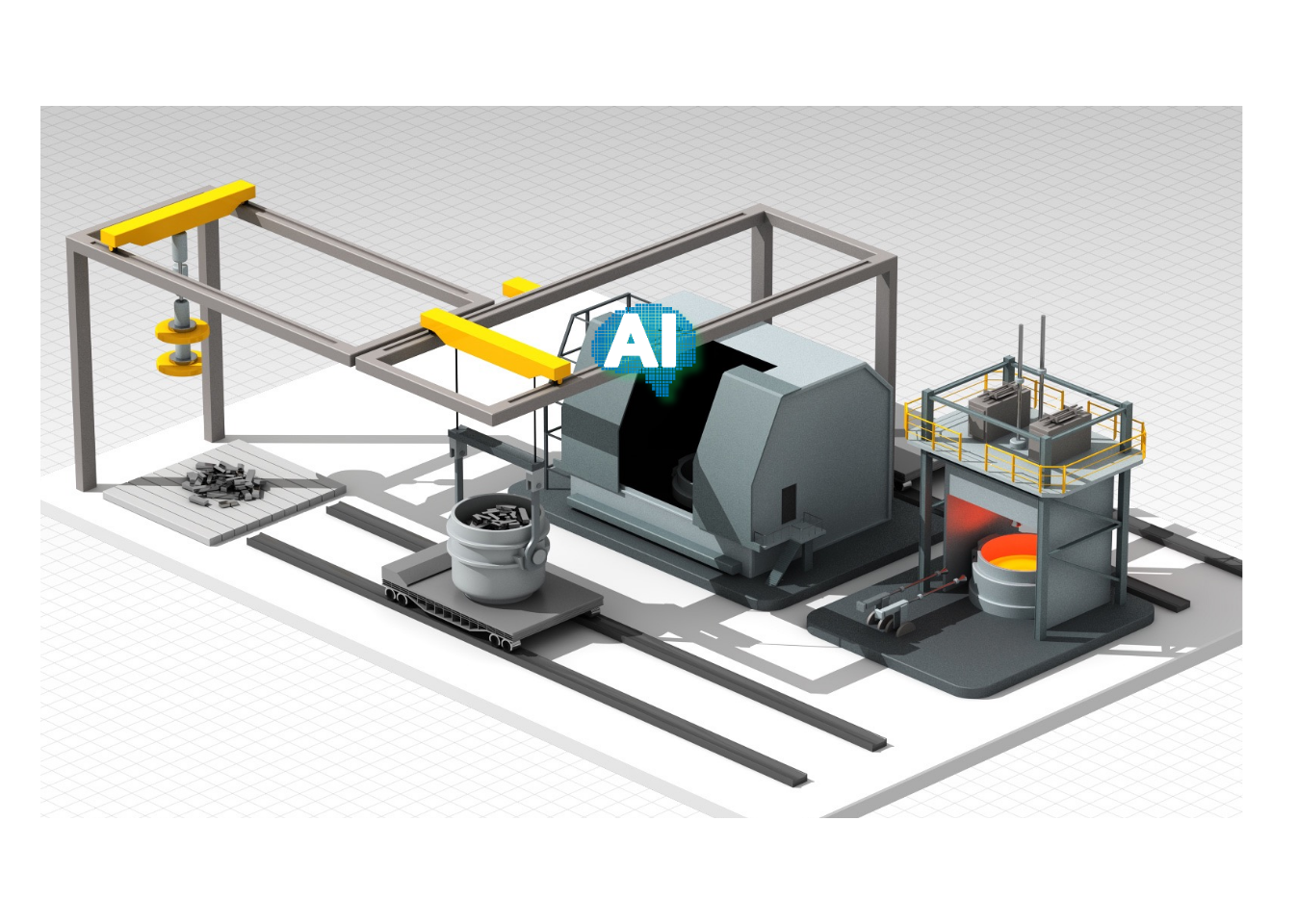
Cement manufacturing process Calcination Furnace
Reducing use of bituminous coal and increased use of recycled fuel
AS-IS
•
Excessive carbon emissions occur when using bituminous coal
•
Difficult to control heat when using recycled fuel to solve excessive carbon emissions, so the amount of bituminous coal used cannot be reduced as much as expected
•
When increasing the amount of recycled fuel, quality control is difficult due to severe fluctuations in heat content
INFINITE OPTIMAL SERIES™
•
Stable heat content control while increasing the ratio of recycled fuel usage
T0-BE
•
While maintaining and improving productivity and quality, increasing the usage of recycled fuel compared to the previous usage and reducing the use of bituminous coal
•
Reducing carbon emissions
Key data
•
Preheating room temperature, Raw material·fuel input amount, Exhaust gas concentration, etc.
※ Actual data required for implementation may vary.
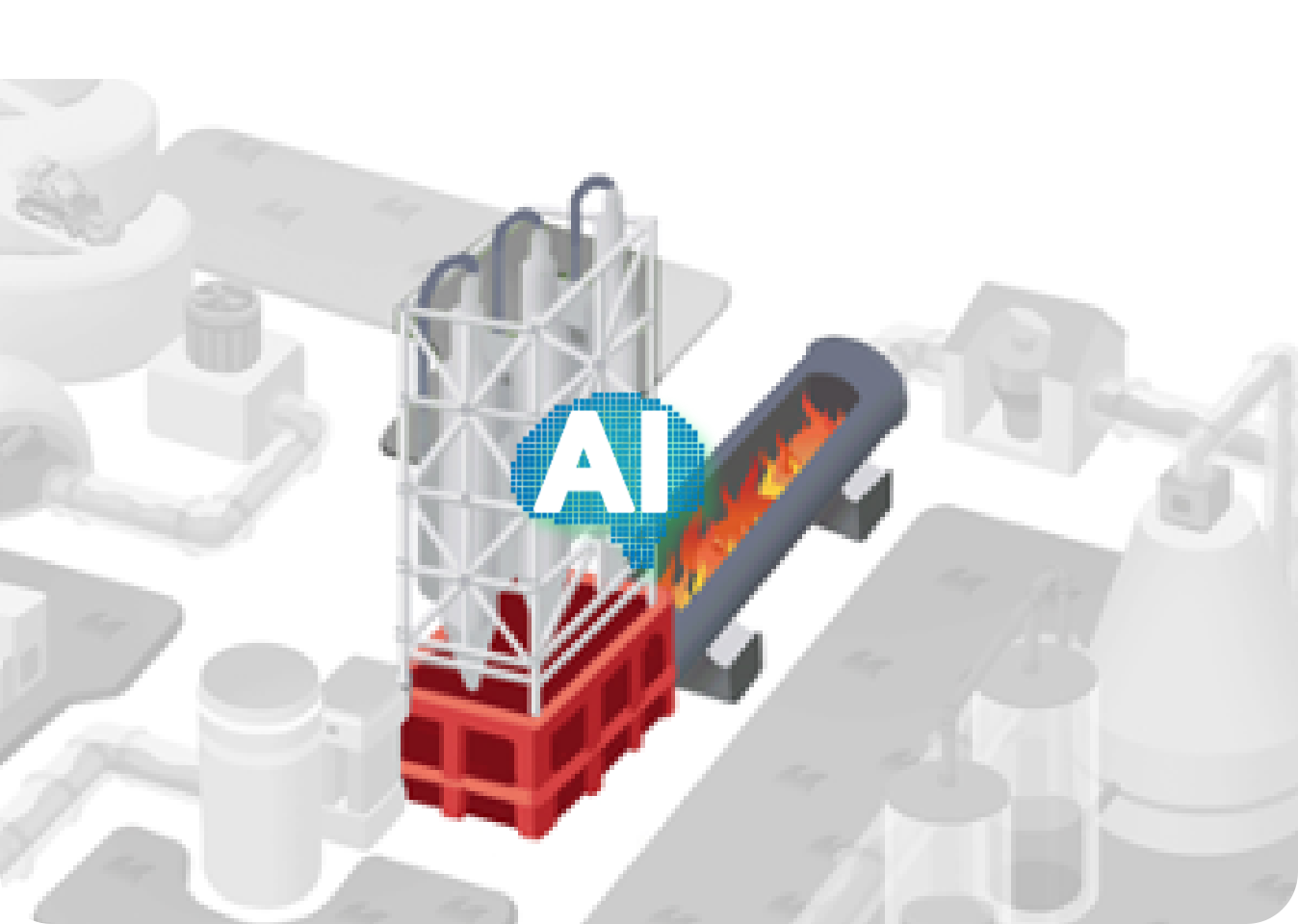
Glass melting Furnace
Stabilization of production and reduction in fuel usage
AS-IS
•
Difficult to determine the optimal fuel input for maintaining the target temperature inside the melting furnace
•
Excessive fuel and electric power usage for preventing defects when there are significant fluctuations in the output
INFINITE OPTIMAL SERIES™
•
Maintain appropriate temperature and control the fuel input according to fluctuations in elution amount
T0-BE
•
Internal temperature standardization in the melting furnace
•
Preemptive temperature control in response to output fluctuations
•
Reduction in fuel input
Key data
•
Output(production quantity), Raw material quantity, Cullet input rate, External temperature, etc.
※ Actual data required for implementation may vary.
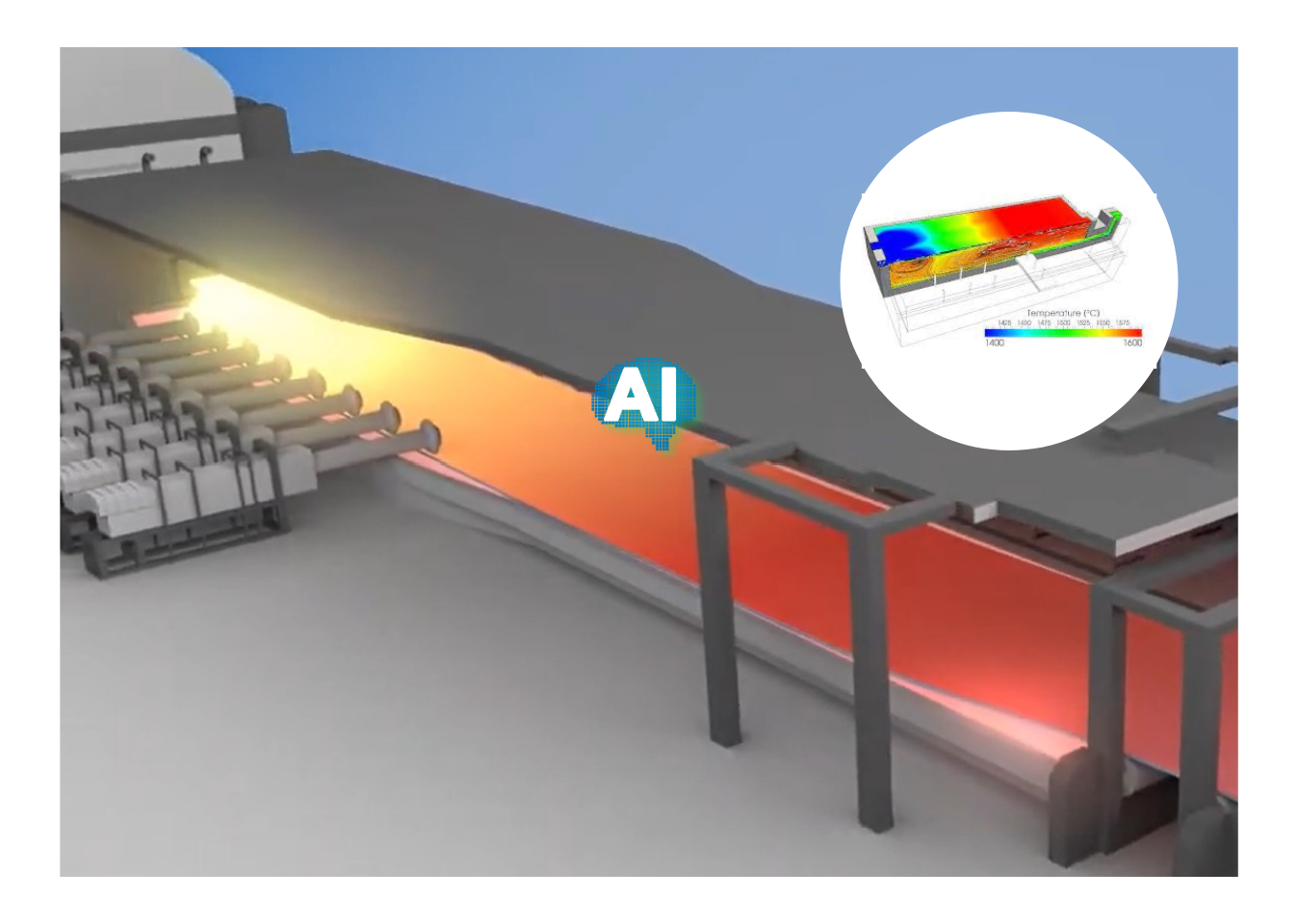
POE(Polyolefin Elastomer) process
Quality improvement and production optimization
AS-IS
•
Real-time measurement is difficult, resulting in a time delay in confirming properties
•
Real-time quality control(stabilization) is difficult during the time required for property confirmation
INFINITE OPTIMAL SERIES™
•
Achieving and stabilizing the target three properties through real-time prediction
T0-BE
•
Real-time prediction of product properties based on raw material input quantity
•
Reduction in product quality variance by operator
•
0.5% increase in daily production compared to before
Key data
•
Raw material input quantity, Internal temperature of the reactor, Oxygen quantity, Operating conditions, Reaction substance ratio
※ Actual data required for implementation may vary.
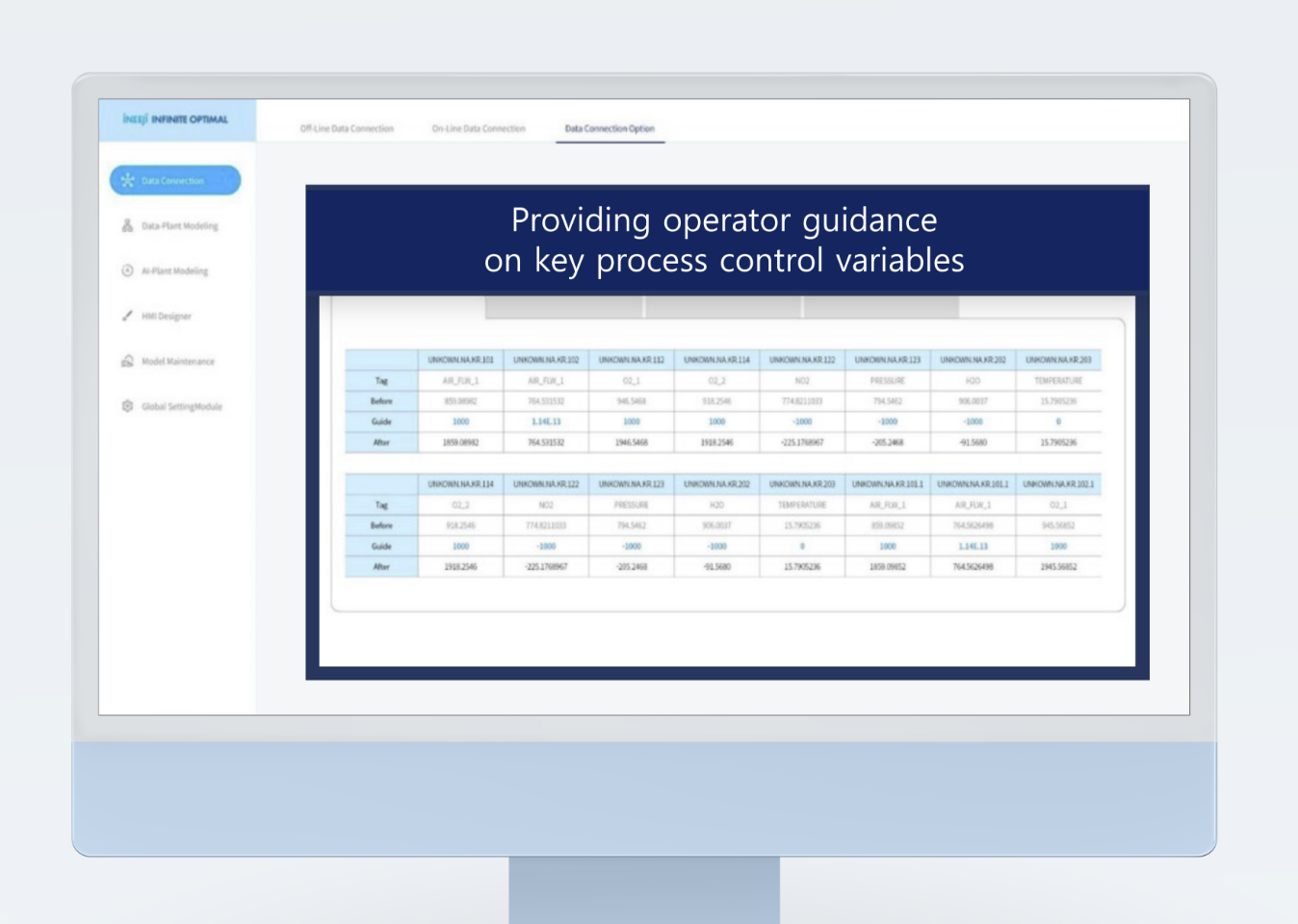
Residue oil Hydro-Desulfurization process
Quality improvement and production efficiency enhancement
AS-IS
•
Time is required for sample collection and confirmation of quality analysis results
•
Difficulty in real-time control until the analysis results are confirmed
INFINITE OPTIMAL SERIES™
•
Quality improvement and reduction in raw material (raw material, steam) usage through quality prediction of major products (diesel, etc.)
T0-BE
•
Reduction in the time for quality verification
•
75% reduction in prediction error compared to the previous prediction model
•
Improved productivity and cost optimization of raw materials (raw materials, steam) through the maintenance of target quality
Key data
•
Internal temperature of the distillation column, Specific section temperatures and flow rates(processing rates), etc.
※ Actual data required for implementation may vary.
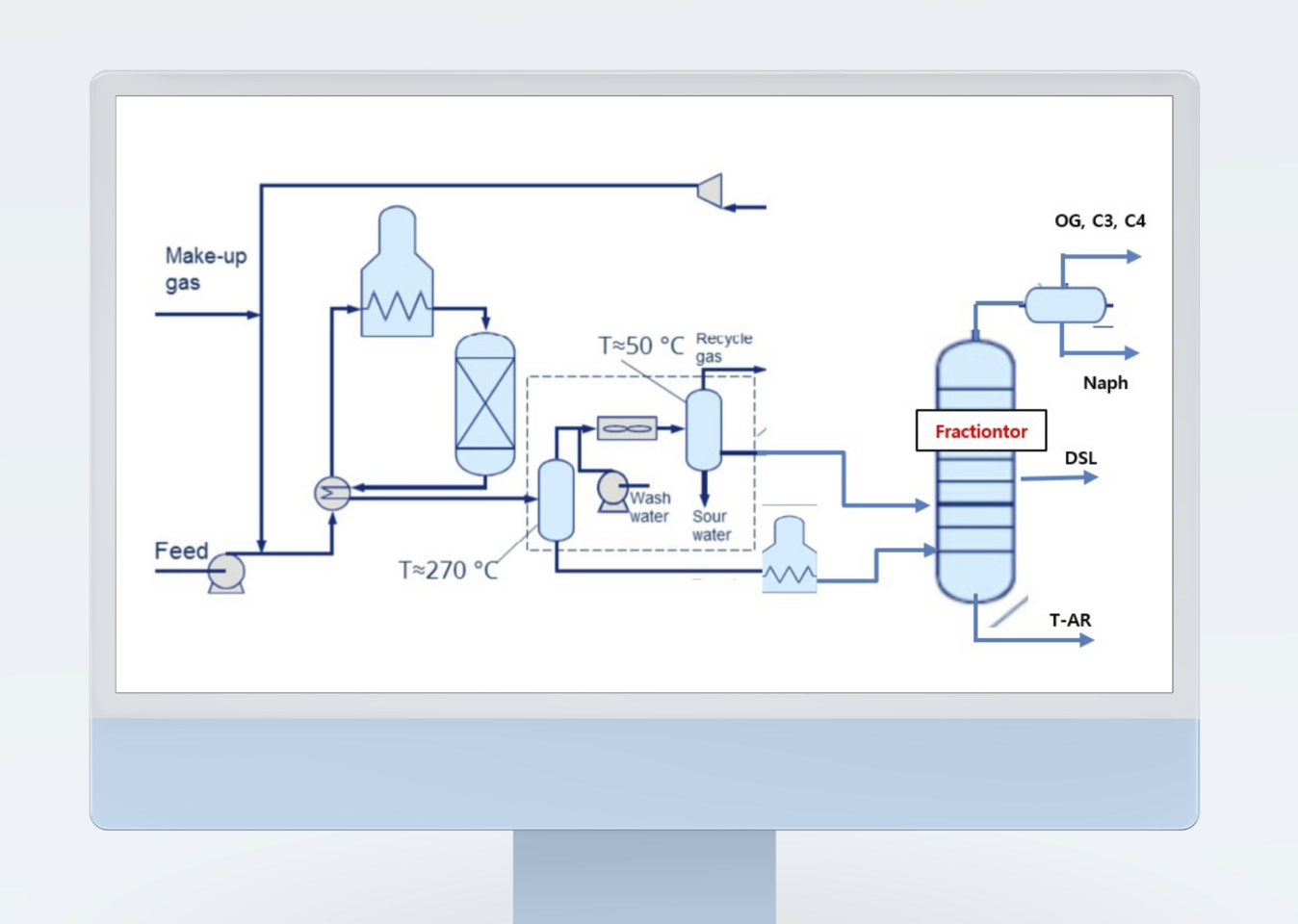
Smart city
Traffic congestion prediction and signal optimization for habitually congested sections on 13 roads in ○○si, Gyeonggi-do
AS-IS
•
Chronic congestion occurs due to increased traffic volume during specific times caused by commuting vehicles between Seoul and Incheon
INFINITE OPTIMAL SERIES™
•
Alleviating traffic congestion in chronic congestion areas through advanced traffic prediction and control
T0-BE
•
Daily traffic volume in the solution application area increased by 4.72% through optimized control of intersection signal times
•
Optimization and visualization of intersection signal timings
Key data
•
Intersection configuration, Signal information, Traffic flow, Vehicle movement speed, The number of waiting vehicles, etc.
※ Actual data required for implementation may vary.
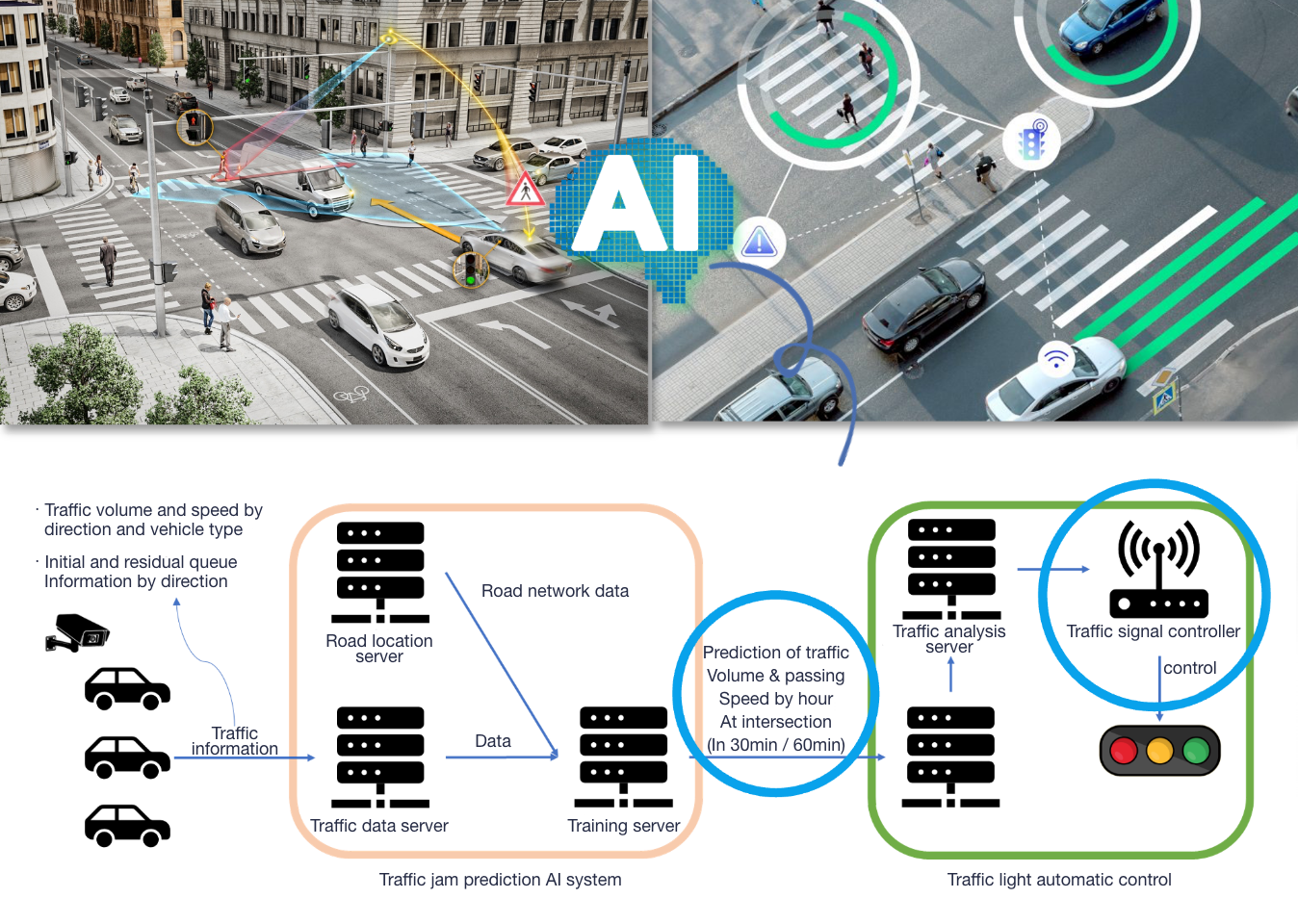
Power Generation
Early detection of thermal power plant boiler tube leaks Ι Prognostics and Health Management(PHM)
AS-IS
•
Detecting tube leaks based on acoustic sensor data, but the accuracy is low, and impossible to detect leaks due to fine cracks
INFINITE OPTIMAL SERIES™
•
Preventing losses due to sudden accidents and equipment downtime
T0-BE
•
Early detection of boiler tube leaks 62 hours earlier than the previous BTLD system
•
Successful detection of fine tube cracks that were not found when detected by sound
•
Improvement in the overall operational efficiency of the boiler
Key data
•
Boiler temperature, Fuel, and Air input quantity, etc.
※ Actual data required for implementation may vary.
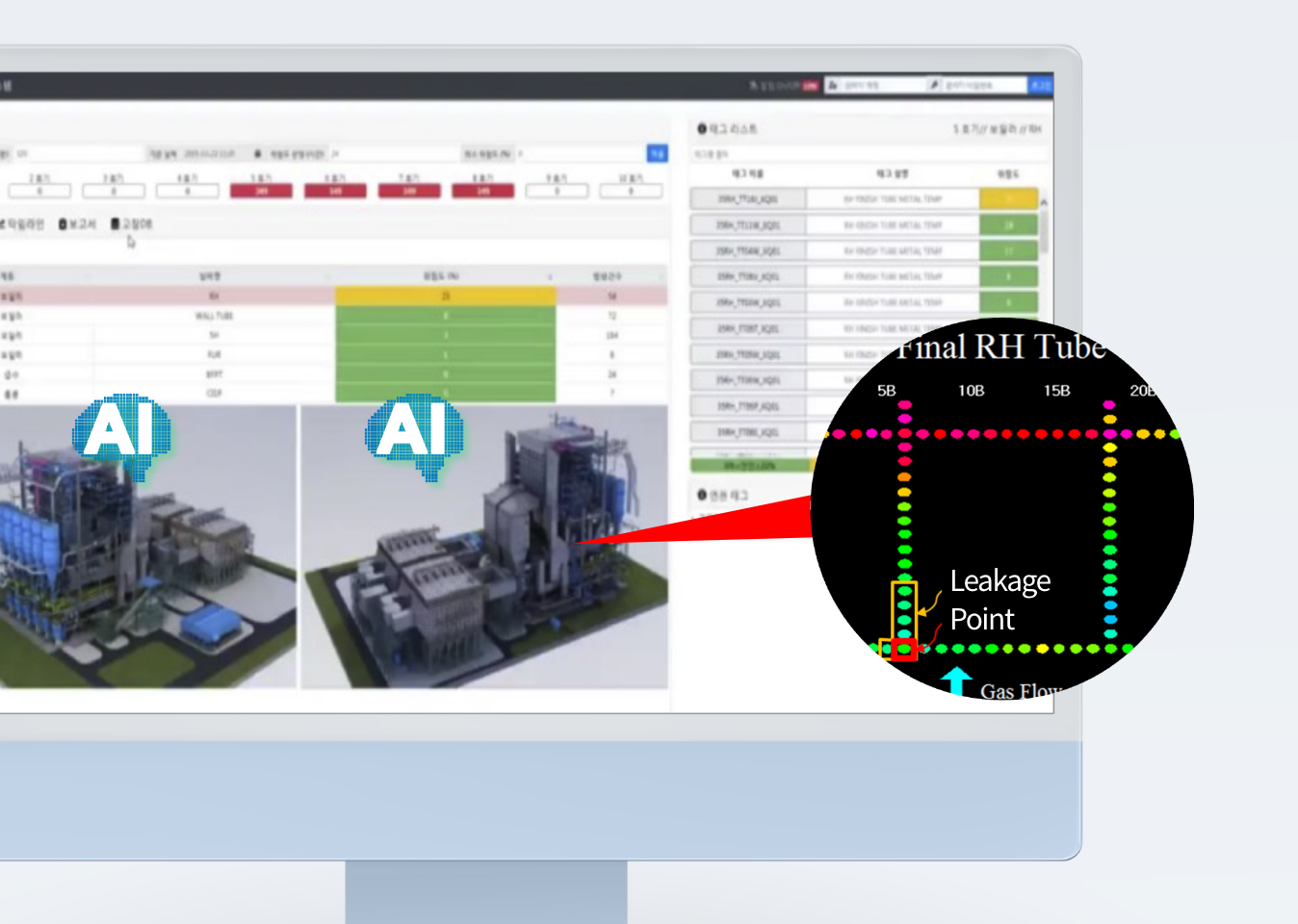